T
George Urban
Image source: History of Germans in Buffalo & Erie County (archivaria.com)
George Urban, Sr. came to Buffalo at age 15 with his parents in 1835. They were among the first German settlers in Buffalo, coming from Morsbrunn, Alsace, in ethnic Germany. After working as a buyer for Henry Colton's store on Main Street, he opened a wholesale flour business at the northeast corner of Genesee and Oak Street. He was a successful businessman, Vice President of the Western Savings Bank, member of the Parks Commission, and father of three, including George Urban, Jr.
When his son joined the business, they named it, George Urban & Son. In 1880, the company incorporated itself as Urban & Co. At that time, it had expanded business under George, Jr. and marketed flour to the East coast of the U.S., including Boston.
George Urban, Sr., retired in 1884 and died in 1887 at age 67.
George Urban, Jr., 1908
Image source: Buffalo Evening News History of Buffalo
George Urban, Jr. entered his father's business in 1866 at age 16. With the success of Urban & Co., the the company constructed its own mill on the northwest corner of Genesee and Oak Street, across the street from the wholesale business. It was the first flour mill in Buffalo to use steel rollers to grind flour instead of millstones.The new mill, completed in 1882, had the capacity of producing 275 barrels of flour per day and the wheat storage capacity of 12,000 bushels.
After his father died, George, Jr., renamed the company, Urban Milling Co., marketing Liberty Flour to commercial buyers. By 1899, the successful company was competing with four other Buffalo flour millers: Banner, Central, Harvey & Henry, Thorton & Chester.
George, Jr., married Ada E. Winspear in 1875 and built a large farm estate on Pine Ridge Road in Cheektowaga. See his Cheektowaga estate over time here. There, in 1883, he hosted fellow Republican politicians at his "log cabin" where the presidential campaign of his friend, Grover Cleveland, began.
He was an early enthusiast of electrical power. Urban and William R. Huntley, an Urban Milling director, founded the Brush Electric Light Co. in 1880, which was Buffalo's first municipal lighting plant. Eventually, this venture was merged into the Buffalo General Electric Co. and the Cataract Power & Conduit Co.
In 1903, the milling company incorporated under the name, George Urban MIlling Co., and sold stock to raise money for construction of a much larger factory complex.
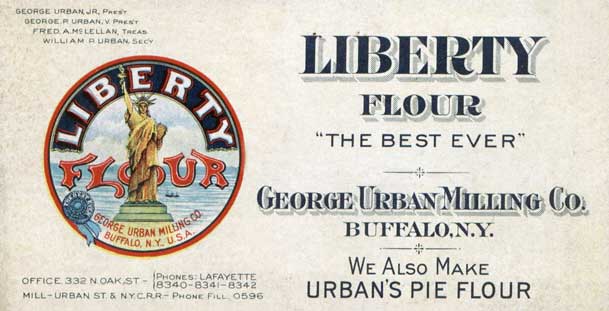
The new Urban mill would be built on land acquired at a sheriff's sale in the 1870s on Buffalo's East Side on Kehr Street. The estimated construction cost of the mill and grain elevator in 1903 was $200,000 ($5,032,300 in 2012 dollars). The location was well-placed, adjacent to the New York Central Beltline tracks. The new mill would have the flour production capacity of 1,200 barrels per day and the 12-compartment elevator capable of storing 60,000 bushels of wheat. In addition to featuring state of the art flour-milling technology, the mill was the first in Buffalo to be entirely powered by electricity.
The new mill opened on September 22, 1903 and was very successful. By 1912, expansion permitted the production of 1,600 barrels of Liberty and Lotus brand wheat and rye flour daily. The company's slogan was, "The Best Ever."
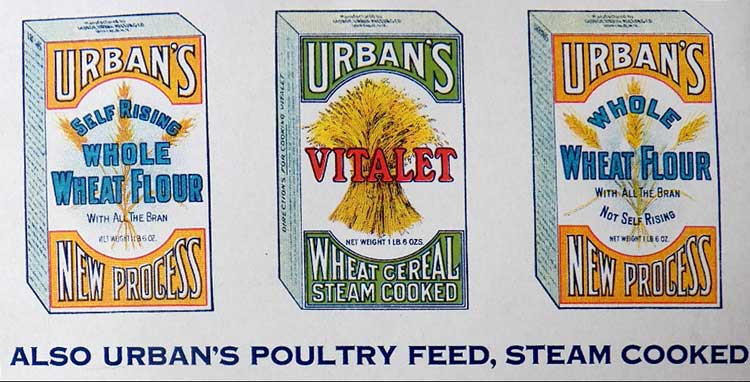
Advertising image of Urban flours. Image source: private collection
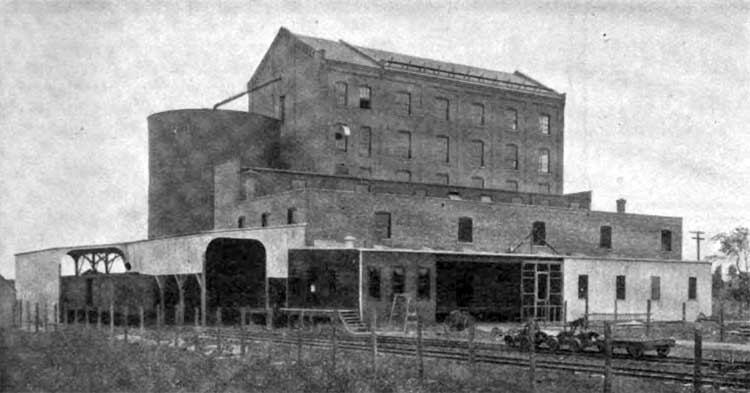
Factory from the railroad tracks, 1904. Image source: American Hay, Flour & Feed Journal
From a Buffalo Express article, November 15, 1903: "The mill building proper is five stories high, each floor being devoted to a particular stage of flour-making. An annex two stories high contains the packing, shipping and storage departments. The mill has its own railroad tracks connecting directly with the New York Central Beltline. These tracks provide all the room required for receiving and handling large quantities of grain daily. Loaded cars are run to the unloading point and are there weighed on track scales. These scales automatically register the gross and net weight. Automatic power shovels unload the grain from the cars into a chute or hopper, whence it is transported underground to the main receiving elevator."
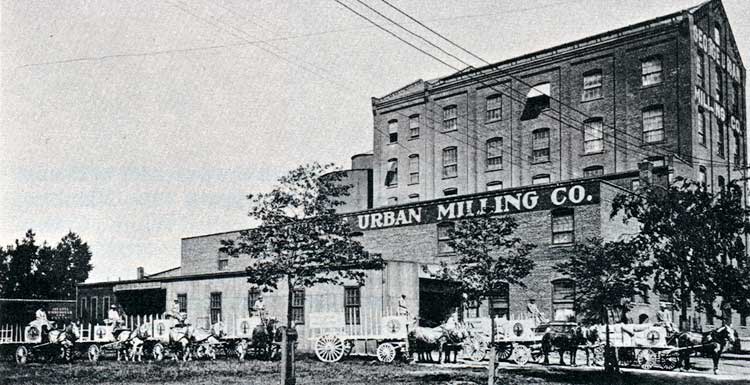
Delivery wagons lined up with Liberty Flour decals, c. 1905. Image source: TBHM
To ensure that every particle of flour was uniform in size, "from the time the wheat is received from the car until it is packed in bags and barrels as flour, it has been conveyed from one part of the building to another, from one machine to another by means of belts, elevators, and spouts and thereby has escaped being broken or frayed at any stage. This is one of the important features of the new mill, the machinery for which was installed by the Nordyke & Marmon Company of Indianapolis under the personal supervision of George A. Sutton, chief millwright, and L.I. Ziegler, chief milling engineer, after plans of operation made by Barnum F. Ortman, head miller for the George Urban Milling Company."
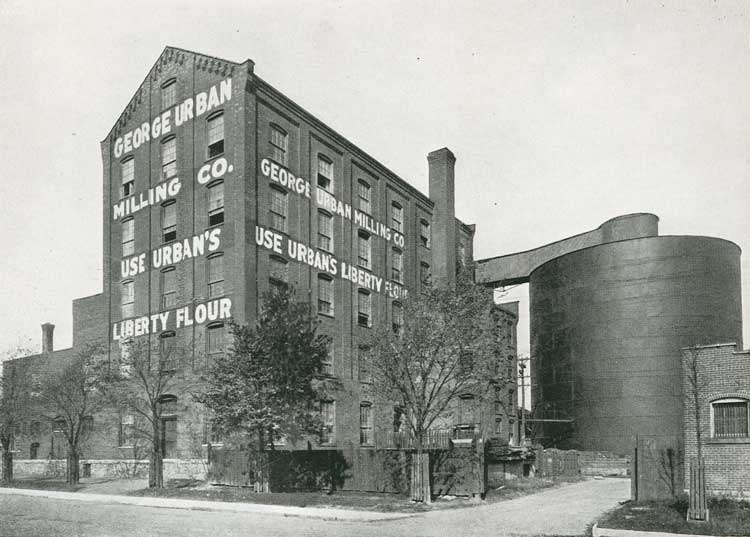
Image source: Buffalo Live Wire, 1912
"From the receiving elevator the grain flows by gravity onto a receiving separator. Here it has its first cleaning. This machine has two methods of separating the grain from the foreign substances which it may contain - one through perforated metal, the other by air... the grain again falls by gravity into an elevator, which carries it to the top of the mill building, where it is spouted and falls by gravity into the 60,000 bushel steel tank. Here it remains until it is wanted for transformation into flour."
Unless otherwise labeled, the interior images below are from The Buffalo Express,November 15, 1903 , BECPL
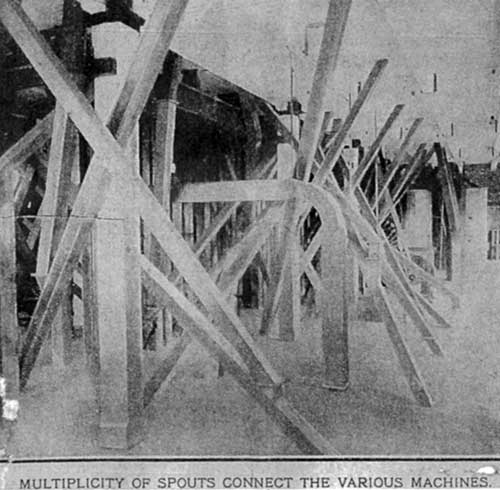
"The storage tank into which the wheat has been conveyed...has twelve compartments. From any or all of these twelve, grain may be drawn as it is wanted for specific purposes. It is discharged from this tank by means of spouts upon flat carrier belts. By these it it taken to the top of the mill building."
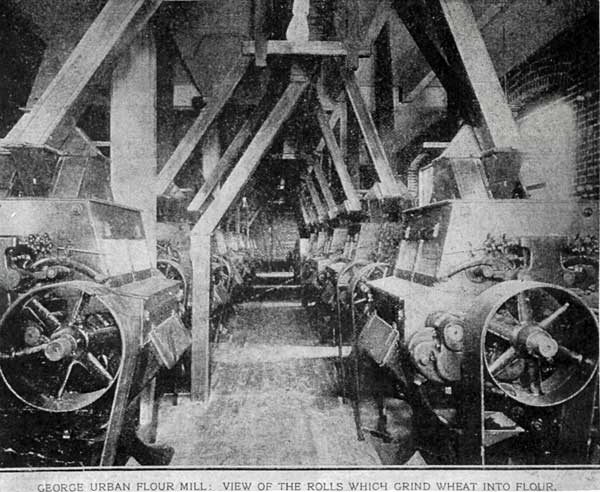
"The wheat is cleaned in two additional ways before it begins the milling process. "As the wheat falls from the supply bin into the first set of rolls - called break rolls - it passed through a governor which controls the supply and makes uniform the feed into the rolls. All rolls, whether break rolls or middling rolls, are contained in close-shut iron frames so that there may be no escape of flour or bran dust from them and no introduction of foreign material from without. Break rolls have corrugated faces and are used for the reduction of the wheat so long as the bran is not clean."
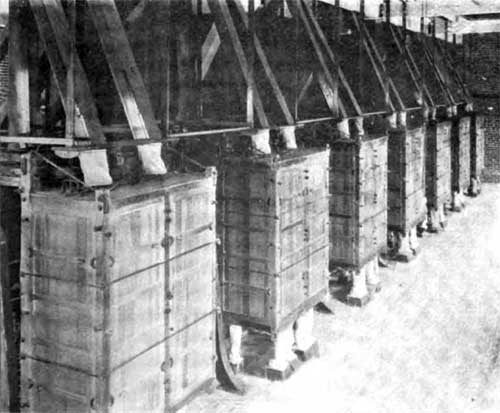
Sifters. Image source: American Hay, Flour and Feed Journal
"Five different reductions are used for this purpose. First the wheat passes through four pairs of coarsely corrugated rolls and is then elevated to the top of the millhouse and by gravity falls to the sifting or bolting machines. These are tall square boxes in appearance and when in operation have a gyrating motion. They are clothed with wire and silk of different meshes and the particles broken by the break rolls are divided into different grades according to their size by being sifted throught these wires and cloths. The coarser particles, especially those containing bran, pass off to the second series of breaks, consisting of four pairs of rolls, after which they are again elevated to the same style of elevating or bolting machines, where the former method of separation is again gone through. This process is repeated through five consecutive operations on break rolls."
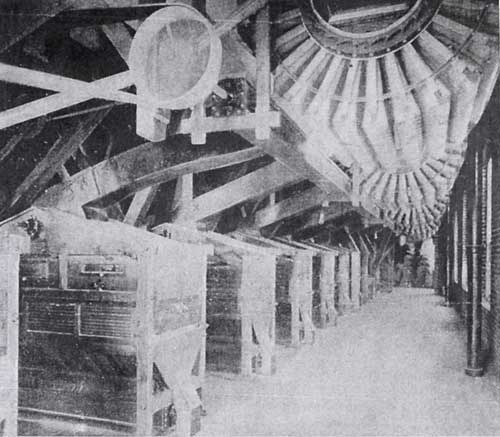
Purifiers
The process used "bolting cloth" in a "flour dresser" to separate the consumer-grade flour, known as middlings or farina, from low-grade flour, which was not sold for human consumption. The farina continued to be processed in the purifers, smooth rollers, and sifters.
"Purifers are large, enclosed machines... Their function is to remove all dark fibrous particles from the farina in its differnt stages and to assist in grading it into proper sizes for rolls. Connected with them are dust collectors and coolers., curious appearing appliances suspended from the ceiling and which revolve slowly, drawing the heat and dust from the purifiers...After having been purified, the farina is subjected to a process of reduction through smooth rolls, so as to flatten out any impurities...the idea being to make a gradual and continous reduction and to avoid heating any particles so that its vitality is impaired."
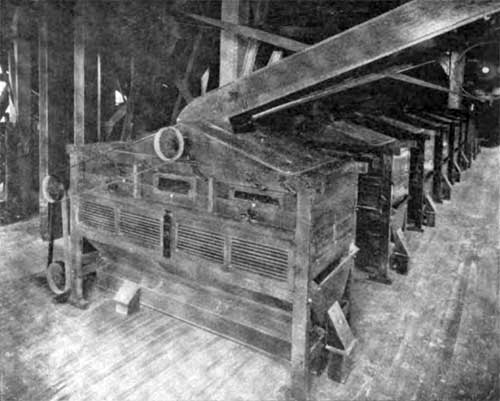
Another view of the purifiers. Image source: American Hay, Flour and Feed Journal
"After each reduction is made on smooth rolls from two to four separations are made in the bolting machines, the finished flour in each case going to the packers and the other particles, depending on size and quality, going to the different systems, thirteen of which are used in this mill. Ten stands of double-roller mills - corrugated and used for breaks - and fourteen double-roller mills for farina reductions - a total of 24 mills- are employed in this process of making the Liberty flour, the 'best flour in the world.' Besides these, there are thirteen purifiers, nine square sifters and six reels and a system of suction fans and dust collectors... In all, there are 240 separations or different kinds of stock under process of production in this mill at all times."
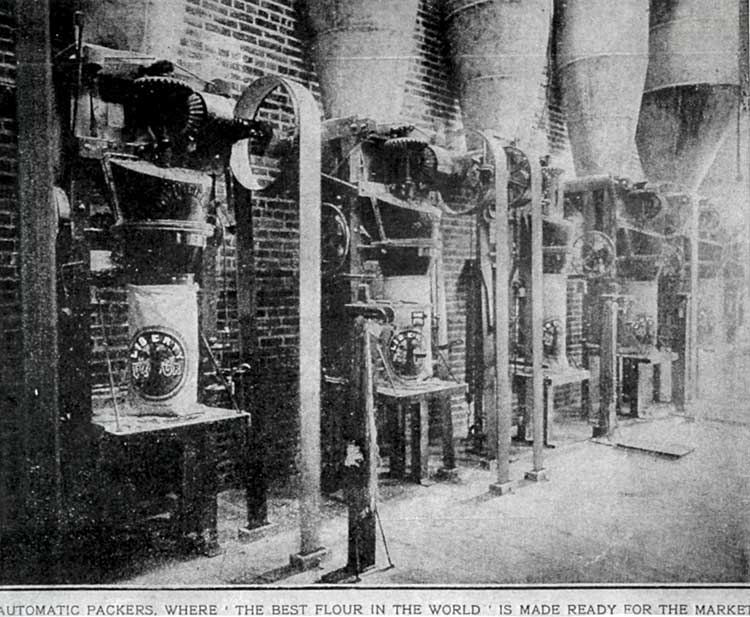
"The whole system is known as the automatic, the grain beign handled automatically from the time it leaves the storage tank until it is deposited into the stock bins...until the finished products are deposited into the receiving bins, there to be drawn into automatic packers...From the packing floor the filled bags and barrels are carried by a continous elevator to the floor below where they are ready for shipment."
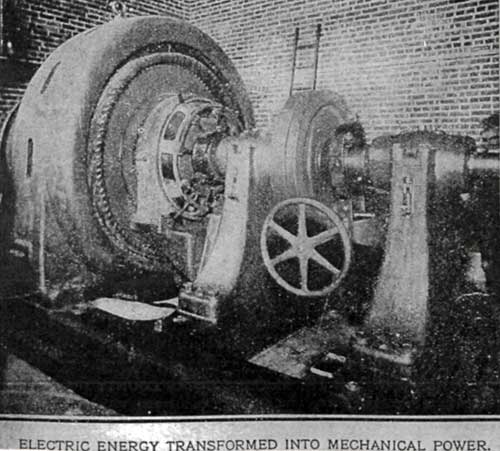
"The power for running this great plant is obtained from Niagara Falls, the electrical energy being transformed into mechanical power by a 400-horsepower synchronous motor, built by the General Electric Company in Schenectady."
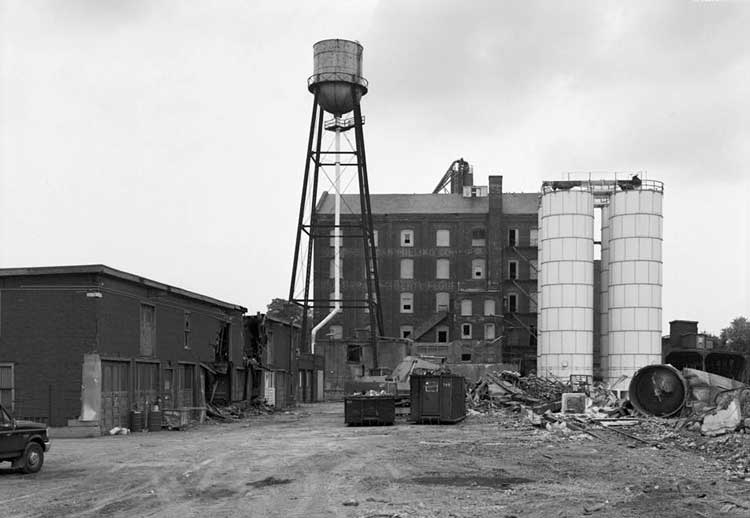
Urban plant in its last days, 1990-91. Image source: Library of Congress HAER
George Urban, Jr., died in 1928 at age 78. His son, George P. Urban, became president of the company and his two sons also came into the business.
At the time of George Urban, Jr.'s death, Buffalo had seven flour mills. By 1930, Buffalo had become the flour milling capital of the U.S., surpassing Minneapolis. Buffalo's daily milling capacity was 40,000 barrels (which, by 1948, had increased to 51,000 barrels daily).
Buffalo millers could choose the best wheat from the huge quantity of midwestern U.S. and Canadian grains that passed through Buffalo's port. The Canadian spring and winter wheats were especially prized and the high-quality flour produced from them accounted for the fact that 42% of Buffalo flour was exported to western Europe.
George Urban Milling survived the Depression; expansions allowed the mill to offer Urban's Pie Flour and Up-and-Up, a self-rising cake flour. The company shipped to eastern markets that included all of New England, New Jersey, and Pennsylvania. In 1940, there were 120 people employed on three 8-hour shifts. By 1946, the daily output was as high as 1,500 barrels a day. In 1951, the company rebuilt and expanded the mill. Up until the 1960s, the company enjoyed continuing success. Then, in 1965, with waning family commitment, the outside directors voted to become a subsidiary of Seaboard Allied Milling, a midwestern organization. Seaboard upgraded the mill and grain bins.
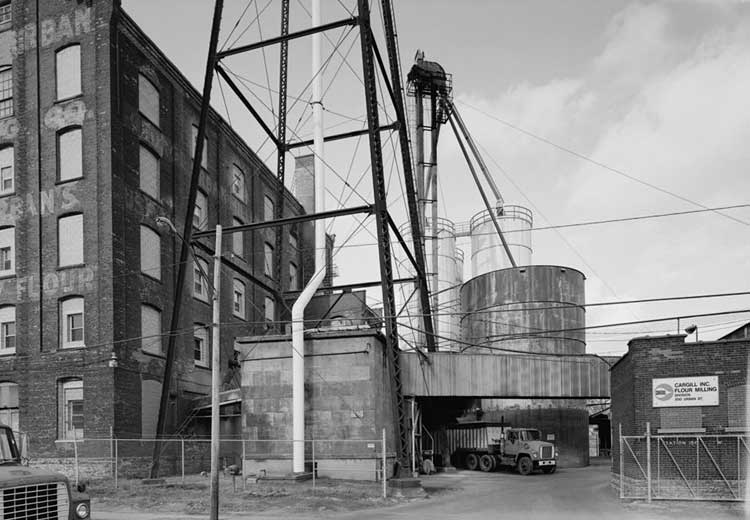
Urban plant in its last days, 1990-91. Image source: Library of Congress HAER
In 1983, Seaboard sold the Urban Milling Company to Cargill. And, in March 1994, Cargill closed the plant. Among the reasons given were the declining animal feed prices; 30% of every bushel of wheat milled goes for feed. Cargill also complained that the factory was obsolete and the location was more expensive than a water-accessible location. Forty-five employees were left to find jobs in the four remaining Buffalo mills (ConAgra, General Mills Flour, Archer Daniels Midland, International Multifoods). By 2001, just two mills remained: General Mills and Archer Daniels Midland.